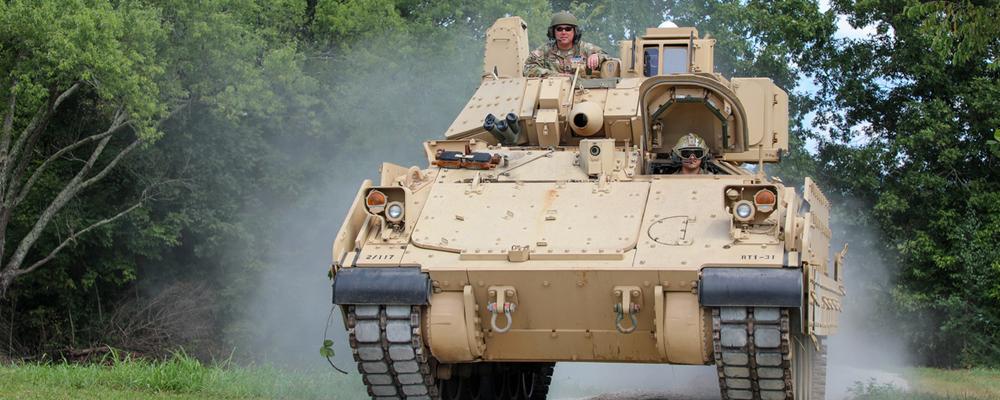
New Ground
By Megan Holbrook & Lt. Col. Casey E. Bain (Ret.)
Army officials are racing to develop the ability to swiftly manufacture critical repair parts at the point of need in austere environments to support the maneuver force.
“Expeditionary manufacturing,” the service’s preferred term for the idea, could reduce the huge logistics tail required to conduct operations overseas, saving valuable resources and lives. It could also lower the number of warfighters needed for convoy security. Cold Spray, a form of 3D printing metal, is among the concepts under development.
Members of the Tennessee Army National Guard’s 278th Armored Cavalry Regiment in August conducted the first soldier-led and implemented CS demonstration with the support of the Army Combat Capabilities Development Command Army Research Laboratory, select industry partners and the University of Tennessee.
ARL has been maturing CS over the past decade. The technology involves spraying fine powders (1-50 micrometers in diameter) at supersonic velocity to a surface. Upon impact, the powder consolidates into a dense solid material.
CS stands out among current repair technologies as it does not require melting the material (as welding does), according to ARL. Recent advances in robotics have enabled the technology to produce factory-grade parts through additive manufacturing.
While CS has been around since the early 1990s, recent advances, thanks to ARL and industry collaboration, have taken the capability further through the development of an expeditionary system that puts the technology in the hands of the warfighter. Soldiers themselves can make repairs swiftly, without having to take platforms out of the fight for extended periods of time.
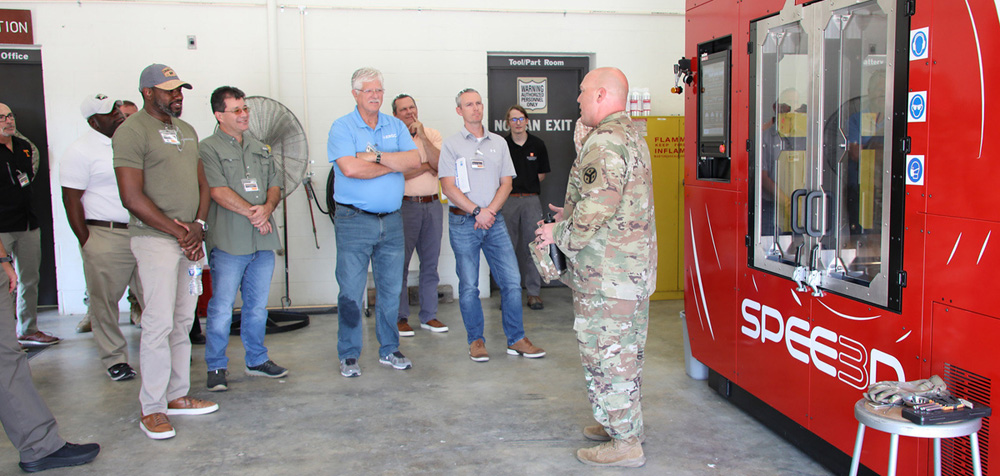
The three-week CS demonstration was a collaborative effort among ARL, the 278th ACR, research and machining experts from the UT, and two leading 3D printing companies, SPEE3D and VRC Metal Systems. Everything took place at the Guard armory in Livingston, Tennessee, which simulated an overseas forward operation base.
Week One was devoted to set-up and technology familiarization for the participants. Week Two was the main training period for the two soldiers leading the demonstration. Neither had any earlier experience with the technology. Week Three included final prep and the demonstration to Army, Navy and U.S. Special Operations Command senior leaders.
The demo featured two CS repairs on a Bradley Fighting Vehicle. The first was a repair of one of the plates from the shroud of the vehicle. One of the soldiers used the VRC CS Brolga-2 Mobile Trailer, which was developed with funds from the Pentagon’s Manufacturing Science and Technology Program, to fill-in and build up material on simulated battle damage.
The second repair was the actual manufacturing, installation and live field test of a critical part, a transmission mount cap. This would enable the vehicle and its crew to remain in the fight instead of being “deadlined” while waiting for a new part. A soldier using the Warp SPEE3D CS system printed the part in about two hours, followed by a brief period of heat treatment and machining by the UT machining experts.
ARL meticulously planned the demonstration over several months to create realistic conditions that allowed soldiers to learn how to apply CS in an expeditionary environment, show off their new skills and then provide feedback. The participating soldiers didn’t hold back.
“As far as the CS process goes, it can seem over complicated at first, but only as much as you allow it to be,” said Sgt. Noah Keith. “I had to relate it to the first time I did welding. When you see a welder, you see what goes into it, the hazards of it and you think to yourself that it’s going to be a lot. So, initially, I was a little bit skeptical.
Cold Spray technology could really be a game-changer on the battlefield.
—Sgt. Noah Keith of the Tennessee Army National Guard's 278th Armored Cavalry Regiment
“But after SPEE3D and VRC team members were sent here to train us, I discovered it was one of the easiest things I have ever learned,” Keith said. “As an Army maintainer, I can definitely say that Cold Spray technology could really be a game-changer on the battlefield.”
“With the supply chain being what it is, parts are not always accessible in the time frames in which we need them,” added Sgt. 1st Class Lee Earps, another participant. “This CS technology enables us to manufacture a short-term fix to get the warfighter through the next mission until the supply system catches up with us on the battlefield where we can provide a permanent part replacement.
“I must admit that I came into this demonstration as a skeptic, but after seeing first-hand what CS capabilities are today, I am leaving the demo as a big advocate for this technology.”
The 278th ACR commander was no less impressed.
“We may fight for an hour to a day and then spend the next 22-hours or so fixing, resting and getting ready for the next fight,” said Col. Donny Hebel. “In these circumstances, having a repair part accessible can often mean the difference between victory and defeat. I’m excited to see where we go from here.”
Megan Holbrook is the communications specialist for the Office of Aerospace and Defense at the University of Tennessee. Retired Army Lt. Col. Casey E. Bain is the program manager for UT’s Office of Aerospace and Defense.
TOP PHOTO: Members of the 278th Armored Cavalry Regiment conduct the first-ever field test of a Bradley Fighting Vehicle with a cold spray manufactured part. (Photo by Sgt. 1st Class Timothy Cordeiro)